|
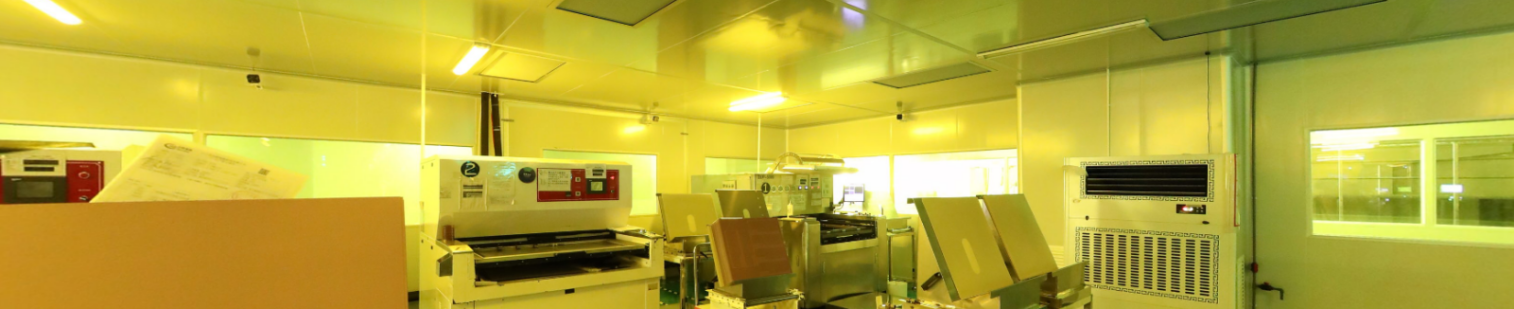 |
|
|
|
|
|
|
|
|
What is Peel Strength in High Frequency PCB? |
|
|
|
|
|
1.The introduction of Peel Strength in High Frequency PCB |
|
|
|
|
|
In high-frequency PCBs, peel strength is crucial as it refers to the adhesive force between the copper layer and the substrate and determines the product's reliability and performance. In high-frequency applications where signal transmission and reliability are key, adhesion must be strong. If inadequate, copper layer may delaminate, causing circuit failure. A concern for engineers as minor adhesion failure can disrupt signal integrity and compromise the system. After all, “peel strength not only determines the durability of a PCB but also decides whether your design can stand the test of time.” |
|
|
|
|
|
|
|
|
|
2.Why Peel Strength Matters in High-Frequency PCBs |
|
|
|
|
High-frequency PCBs, commonly used in applications such as 5G networks, radar systems, and satellite communications, demand exceptional performance under extreme conditions. These boards often face challenges such as rapid temperature changes and high-speed signal transmissions. In such scenarios, poor peel strength can result in copper traces peeling off the substrate, causing irreparable damage to the PCB. |
|
|
|
|
|
|
|
|
|
3.Factors Influencing Peel Strength in High-Frequency PCBs |
|
|
|
|
Several factors influence peel strength in high-frequency PCBs, including the type of substrate material, the thickness and surface treatment of the copper foil, and the manufacturing process. High-frequency PCBs often use specialized materials like PTFE or ceramic-filled laminates. Engineers must carefully select materials and optimize processes to achieve the desired peel strength while maintaining signal integrity. |
|
|
|
|
|
|
|
|
|
4. Superior Peel Strength Characteristics of Rogers RO3035 |
|
|
|
|
Rogers RO3035 high-frequency PCB exhibits outstanding performance in peel strength, with a Copper Peel Strength of 10.2. The Rogers RO3035 PCB board (2-layer, thicknesses of 10 mil or 20 mil) is a ceramic-filled PTFE material specifically designed for high-frequency applications, featuring excellent dielectric properties, thermal stability, and mechanical adhesion. Below, we will analyze the data to highlight its significant advantages in peel strength and other benefits. |
|
|
|
|
|
|
|
|
|
4.1 Peel Strength Data Comparison |
|
|
|
|
Here is the RO3035 Datasheet's peel strength (using 1 oz copper foil as a benchmark) compared to that of other common materials. |
|
|
|
|
Material Type |
Peel Strength (N/mm) |
Temperature Range (°C) |
Stability of Characteristics |
RO3035 |
1.05 - 1.15 |
-40 to 150 |
Extremely high |
RO4350B |
1.0 - 1.1 |
-40 to 150 |
High |
FR4 (Common Substrate) |
0.8 - 1.0 |
-40 to 120 |
Poor |
PTFE (Common PTFE Substrate) |
0.6 - 0.8 |
-40 to 150 |
Relatively low, prone to delamination |
|
|
|
|
|
|
|
|
|
|
Data Analysis: |
|
|
|
|
RO3035 Ranks First in Peel Strength:
The peel strength of RO3035 reaches over 1.05 N/mm under normal conditions, surpassing other high-frequency materials (such as RO4350B) and traditional substrates (like FR4). Compared to standard PTFE materials, its peel strength is enhanced by 50%, making it significantly more suitable for demanding high-frequency applications.
RO3035 Exhibits Excellent High-Temperature Performance:
RO3035 maintains stable peel strength at temperatures up to 150°C, whereas FR4 and standard PTFE materials are prone to delamination or a sharp decline in adhesion under high temperatures due to thermal expansion mismatch. |
|
|
|
|
4.2 The Typical Value of RO3035 |
|
|
|
|
Key Features |
Details |
Dielectric Constants |
Dk of 3.5 +/- 0.05 at 10 GHz/23°C |
Dissipation Factor |
0.0015 at 10 GHz/23°C |
Thermal Stability |
Td > 500°C |
Thermal Conductivity |
0.5 W/mK(50℃) |
Moisture Absorption |
0.04% |
Thermal Expansion Coefficients (X axis) |
17 ppm/°C (-55 to 288°C) |
Thermal Expansion Coefficients (Y axis) |
17 ppm/°C (-55 to 288°C) |
Thermal Expansion Coefficients (Z axis) |
24 ppm/°C (-55 to 288°C) |
Volume Resistivity |
10<sup>7</sup> MΩ.cm (COND A) |
Surface Resistivity |
10<sup>7</sup> MΩ (COND A) |
|
|
|
|
|
|
|
|
|
|
4.3 Value of RO3035 in Practical Applications |
|
|
|
|
5G Communication Equipment:
High-frequency signal transmission requires materials with strong adhesion to prevent copper foil delamination, ensuring signal integrity. RO3035 provides an ideal solution.
Aerospace and Radar Systems:
In extreme temperatures and vibration environments, the peel strength and thermal stability of RO3035 ensure the reliability and longevity of circuit boards.
High-Power RF Modules:
Under high temperatures and high-power conditions, the peel strength of RO3035 effectively prevents copper foil delamination, ensuring the stability of circuit functionality.
Based on the above data and analysis, it is apparent that RO3035 high-frequency PCBs excel in peel strength and maintain stability across a wide temperature range. |
|
|
|
|
|
|
|
|
|
5. How to Optimize Peel Strength |
|
|
|
|
5.1 Material Selection
Use high-quality substrates and copper foils with proven adhesion properties.
5.2 Surface Treatment
Apply treatments like chemical roughening or plasma etching to enhance adhesion between layers.
5.3 Thermal Management
Design PCBs to handle thermal expansion and contraction without straining the adhesive bond.
5.4 Manufacturing Precision
Follow strict process controls during lamination to prevent defects that weaken peel strength.
By implementing these strategies, engineers can avoid the catastrophic failure of PCBs in demanding applications. |
|
|
|
|
|
|
|
|
|
6.Final Thoughts |
|
|
|
|
Peel strength is a foundational property that directly impacts the durability and functionality of high-frequency PCBs. It bridges the gap between material selection, manufacturing processes, and long-term reliability. For engineers working with high-frequency technologies, mastering the art of peel strength optimization is essential to deliver designs that withstand the test of time and high performance. |
|
|
|
|
|
|
|
|
|
|
|
|
|
|
|
|
|
|
|
|
|
|
|
|
|
|
|
|
|
|
|
|
|
|
|
|