|
|
|
|
|
|
|
|
|
Heavy Copper FPC Flexible PCB Built On 2 layer Polyimide at 0.3mm Thick with 2oz Copper from Shengyi |
|
|
(FPC’s are custom-made products. The picture and parameters shown are for reference only.) |
|
|
|
|
|
General description |
|
|
This 2-layer polyimide flexible PCB (FPC) features a robust 0.3mm thick construction with heavy 2oz copper layers, engineered specifically for AC power applications. Utilizing high-quality Shengyi base laminate, the design incorporates a 0.1mm FR-4 stiffener on the backside to enhance mechanical stability in high-current environments. Manufactured to IPC 6012 Class 2 standards from customer-provided Gerber files, this polyimide flexible printed circuit combines the durability needed for power systems with the adaptability of polyimide-based flex technology. The FR-4 stiffener provides crucial structural support while maintaining the board's flexibility in non-reinforced areas. |
|
|
|
|
|
Parameter and Data Sheet |
|
|
Size of Flexible PCB |
130.66 X 40.67mm |
Number of Layers |
2 |
Board Type |
Flexible PCB |
Board Thickness |
0.30mm |
Board Material |
Polyimide 50µm |
Board Material Supplier |
ITEQ |
Tg Value of Board Material |
60℃ |
|
PTH Cu thickness |
≥20 µm |
Inner Iayer Cu thicknes |
N/A |
Surface Cu thickness |
70 µm |
|
|
Coverlay Colour |
Yellow |
Number of Coverlay |
2 |
Thickness of Coverlay |
25 µm |
Stiffener Material |
FR-4 |
Stiffener Thickness |
0.2mm |
|
|
Type of Silkscreen Ink |
IJR-4000 MW300 |
Supplier of Silkscreen |
TAIYO |
Color of Silkscreen |
White |
Number of Silkscreen |
1 |
|
Peeling test of Coverlay |
No peelable |
Legend Adhesion |
3M 90℃ No peeling after Min. 3 times test |
|
Surface Finish |
Immersion Gold |
Thickness of Nickle/Gold |
Au: 0.03µm(Min.); Ni 2-4µm |
RoHS Required |
Yes |
Famability |
94-V0 |
|
Thermal Shock Test |
Pass, -25℃±125℃, 1000 cycles. |
Thermal Stress |
Pass, 300±5℃,10 seconds, 3 cycles. No delamination, no blistering. |
Function |
100% Pass electrical test |
Workmanship |
Compliance with IPC-A-600H & IPC-6013C Class 2 |
|
|
|
|
|
|
.jpg) |
|
|
|
|
|
Features and Benefits
1. Excellent flexibility
2. Reducing the volume
3. Weight reduction
4. Consistency of assembly
5. Increased reliability
6. Low cost
7. Continuity of processing
8. The end can be whole soldered
9. On-time service
10. Quick Lead time: 3-5 days |
|
|
|
|
|
Applications |
|
|
General purpose LED soft light strip, mobile phone antenna flex board, industrial control, temperature controller soft board |
|
|
|
|
|
Copper Foils |
|
|
There are two different types of copper foils: Electro-Deposited (ED) copper foils and Rolled and annealed (RA) copper foils.
Electro-deposited (ED) copper foil is manufactured through an electrolytic process where copper is plated onto a rotating stainless steel drum immersed in a solution containing high-purity copper anodes. The foil thickness is controlled by adjusting the drum's rotational speed during plating, after which the copper is peeled and coiled. This process produces foil with distinct surface properties: one side remains exceptionally smooth (drum side), while the opposite side develops a controlled roughness to enhance bonding with substrate materials.
The electrolytic deposition process creates a vertical grain structure that provides high tensile strength but limited ductility, making ED copper unsuitable for applications requiring repeated flexing. Standard thickness options for flexible circuits include 17.5μm (0.5 oz), 35μm (1 oz), 70μm (2 oz), 105μm (3 oz), and 175μm (5 oz). The unique grain orientation influences both mechanical performance and etching characteristics in PCB fabrication processes.
|
|
|
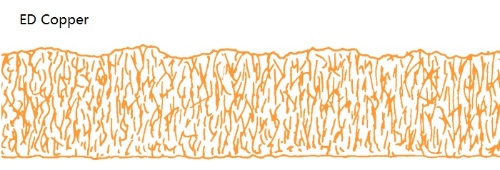 |
|
|
|
|
|
RA Copper |
|
|
This copper is a rolled and annealed copper foil. It is made from electrolytically deposited cathode copper, which is melted and cast into ingots. First, the ingots are hot - rolled to a specific size and then milled on all surfaces. Subsequently, the copper undergoes cold - rolling and annealing processes until the desired thickness is achieved. Unlike electro - deposited copper, rolled and annealed copper has a horizontal grain structure, as depicted below. This horizontal grain structure endows it with significantly higher flexibility and better flex life endurance compared to ED copper. Thus, RA copper is always the preferred choice for dynamic applications. However, a drawback of RA copper is that its bonding surface is rather smooth, resulting in relatively low adhesion. Nevertheless, the bond can be improved by applying an electrolytic copper flash, without degrading the flexing properties of the copper foil. Common foil thicknesses for flexible circuits are 17.5, 35, 70, 105 and 175 µm (equivalent to 0.5, 1, 2, 3 and 5 oz.).
|
|
|
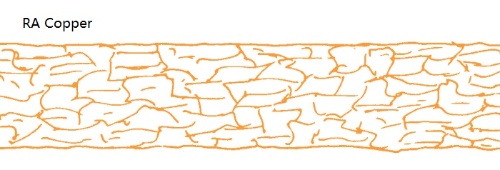 |
|
|
|
|
|
More Displays of Heavy Copper Flex |
|
|
.jpg) |
|
|
|
|
|
.jpg) |
|
|
|
|
|
|
|
|
|
|
|
Hot Tags:
Heavy Copper Flex |
2-layer polyimide FPC |
0.30mm Flexible PCB |
PCB for AC power applications |
FR-4 stiffener Flexible PCB |
|
|
|